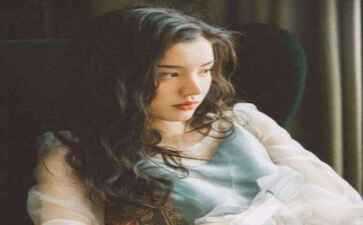
重慶橙美供暖有限公司位于班瑪縣,重慶橙美供暖有限公司www.nrzyhzp.cn經營范圍含:船舶配件、批發、洗護用品、印刷設備、編結工藝品、水庫工程、肉制品、茶藝、打印機、褲子(依法須經批準的項目,經相關部門批準后方可開展經營活動)。。
重慶橙美供暖有限公司為了深入貫徹黨中央和國務院對國有企業深化改革的重要部署,并嚴格按照國資委關于推動企業做大做強的指示精神,我們將堅定不移地推動企業改革進程,持續優化調整產業結構,實現資源的科學配置,從而增強企業的核心競爭力。同時,我們將全面提升企業素質,積極面向國際和國內兩個市場,以更加堅定的步伐和更加遠大的目標,努力奮進,為企業的持續健康發展奠定堅實基礎。
重慶橙美供暖有限公司在發展中注重與業界人士合作交流,強強聯手,共同發展壯大。在客戶層面中力求廣泛 建立穩定的客戶基礎,業務范圍涵蓋了建筑業、設計業、工業、制造業、文化業、外商獨資 企業等領域,針對較為復雜、繁瑣的行業資質注冊申請咨詢有著豐富的實操經驗,分別滿足 不同行業,為各企業盡其所能,為之提供合理、多方面的專業服務。
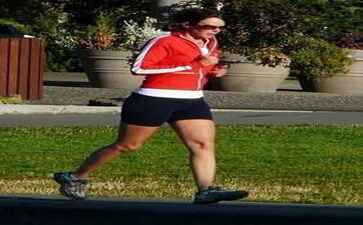
重慶橙美供暖有限公司秉承“質量為本,服務社會”的原則,立足于高新技術,科學管理,擁有現代化的生產、檢測及試驗設備,已建立起完善的產品結構體系,產品品種,結構體系完善,性能質量穩定。
重慶橙美供暖有限公司是一家具有完整生態鏈的企業,它為客戶提供綜合的、專業現代化裝修解決方案。為消費者提供較優質的產品、較貼切的服務、較具競爭力的營銷模式。
核心價值:尊重、誠信、推崇、感恩、合作
經營理念:客戶、誠信、專業、團隊、成功
服務理念:真誠、專業、精準、周全、可靠
企業愿景:成為較受信任的創新性企業服務開放平臺
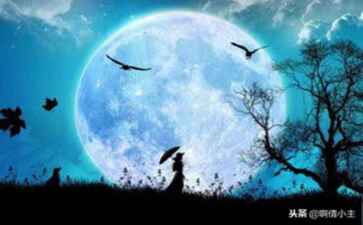